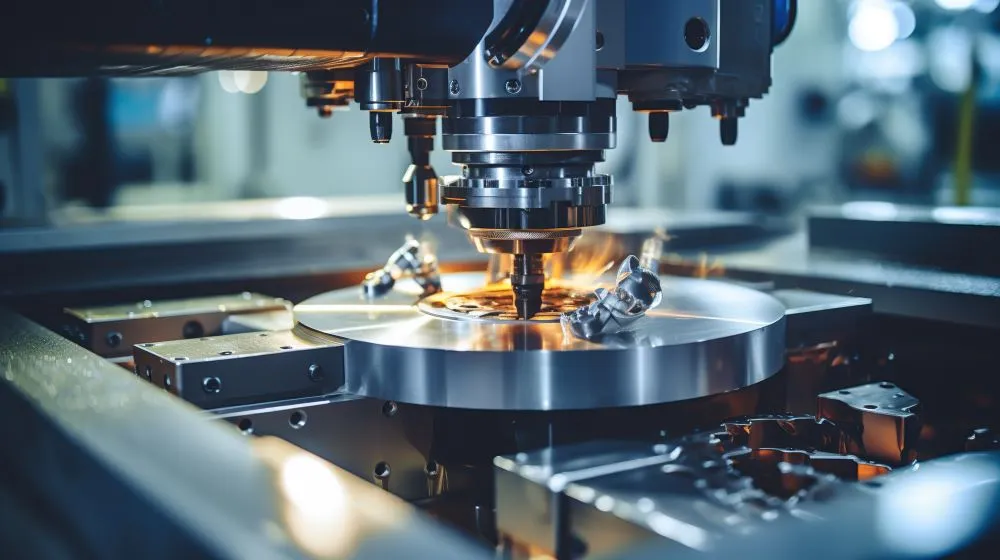
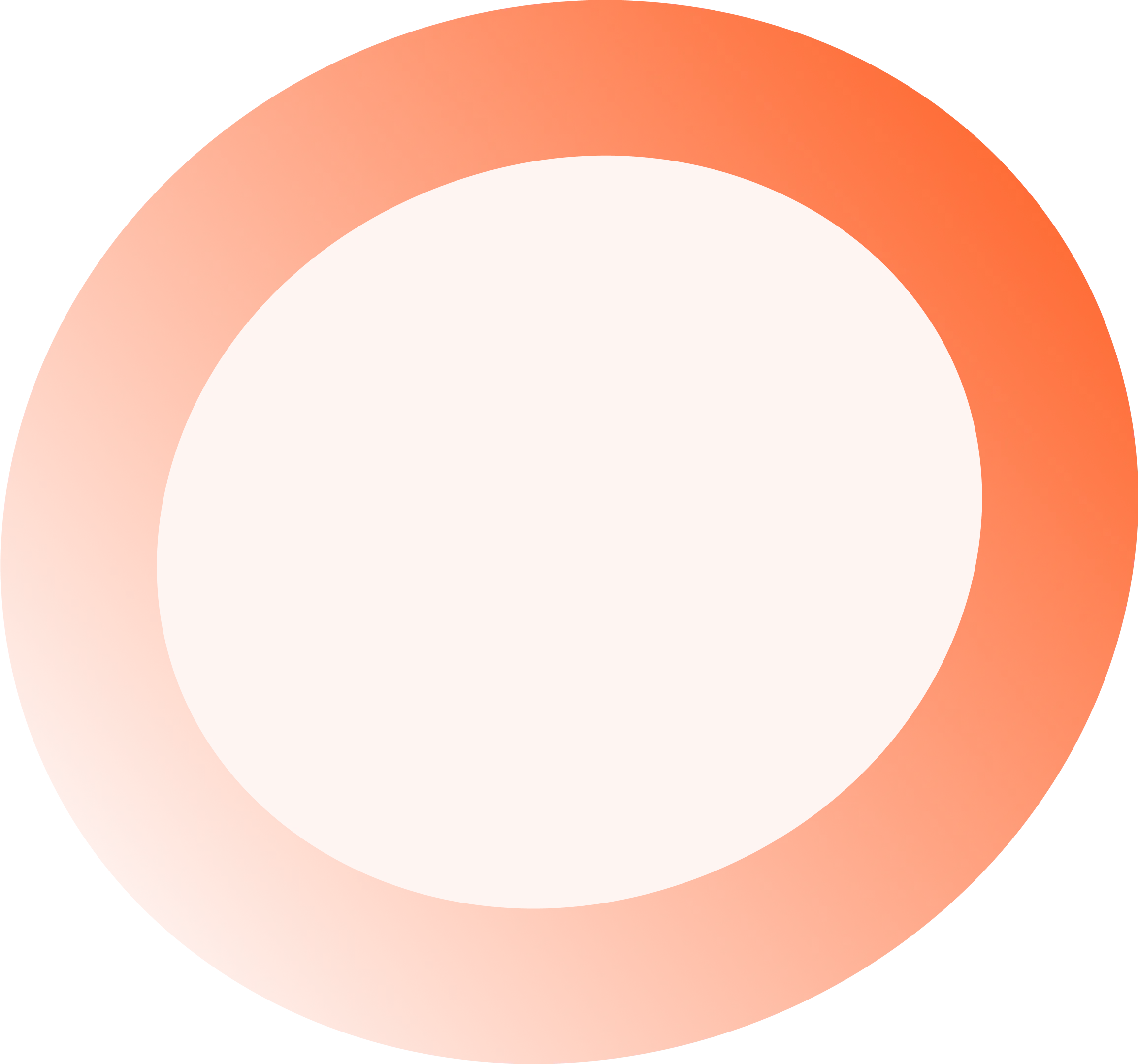
The Art of Precision Machining for Castings
Be it the transportation industry, automation, or medical sciences, precision machining stands behind the growing success of multiple sectors.
Starting right from the basics, precision machining for castings is no less than a meticulous art that transforms raw castings into high-performance components. The process is kickstarted with a raw casting which is refined into a finished component that meets exact specifications.
Precision machining involves removing excess material, smoothing surfaces, and achieving tight tolerances using advanced tools and techniques like CNC (Computer Numerical Control) machining, turning, milling, and grinding. The goal is to ensure the casting meets the expected functional, aesthetic, and performance criteria. Let’s take a deeper look into the role of precision machining in this process.
Why is Precision Machining Essential After Casting?
Castings alone rarely meet the stringent requirements of modern applications. As a result, precision machining becomes a vital step for manufacturing precise components that successfully fulfill their purpose.
1. Achieving Dimensional Accuracy
As castings are produced by pouring molds with liquified metal, it can lead to slight dimensional inconsistencies due to factors like cooling shrinkage, mold imperfections, or material flow issues. Precision machining removes excess material, allowing the part to meet exact tolerances as required by engineering specifications. This is especially critical in industries like aerospace and medical devices, where even minute deviations can compromise performance.
2. Enhancing Surface Finish
The surfaces of cast components often retain rough textures, scaling, or residues from the mold. These are unsuitable for applications requiring low friction or smooth contact surfaces, such as bearings or sealing surfaces. Precision machining uses different techniques like EDM, CNC machining, USM, etc. to produce uniform surfaces. A smoother finish reduces wear and tear, increases operational efficiency, and extends the component's lifespan.
3. Improving Fit and Functionality
Cast parts need to integrate seamlessly into assemblies, whether it’s an engine block or a turbine housing. However, the as-cast condition may include slight distortions or warping that prevent perfect alignment. Machining ensures precise dimensions and alignment for features like holes, threads, and slots. This guarantees that components fit together accurately, preventing issues like vibration, misalignment, or reduced efficiency in mechanical systems.
4. Accommodating Complex Geometries
Casting processes are excellent for creating the general shape of a component but fall behind in their ability to produce fine details or intricate geometries like internal channels, precise edges, or undercuts. Precision machining enables the creation of these detailed features, tailoring the cast part to meet specific functional or aesthetic requirements. For example, turbine blades with optimized aerodynamic profiles are often finished using machining processes after casting.
5. Ensuring Material Integrity and Performance
Castings can contain internal defects such as porosity, inclusions, or uneven density caused by variations in cooling rates or impurities in the molten metal. Machining removes the outer layer and exposes the clean, defect-free material beneath. Additionally, it allows engineers to identify and address potential weak points that could compromise the component under stress, ensuring it meets performance and safety standards.
By combining the strength of castings with the precision of machining, Sevenloop creates parts that are not only functional but also durable. With this synergy, we provide high-performance components across industries, such as automotive, aerospace, defense, industrial goods, agriculture, and mining, where precision is non-negotiable.
5 Cutting-Edge Precision Machining Techniques
Precision machining seamlessly combines technology and craftsmanship. The following modern machining techniques are the most efficient methods to produce high-quality defect-free castings.
CNC Machining
This method uses automated control systems to guide cutting tools with exceptional accuracy. Multi-axis CNC machines, such as 3-axis or 5-axis models, can handle intricate geometries, enabling the production of complex parts for industries like aerospace and automotive. Integration with CAD/CAM software further enhances the efficiency and precision of the process, making it a reliable choice for achieving tight tolerances.
Electrical Discharge Machining
For materials that are challenging to machine conventionally, Electrical Discharge Machining (EDM) offers a specialized solution. This process removes material using electrical discharges between an electrode and the workpiece, allowing for the creation of sharp edges, fine holes, and complex shapes without mechanical stress. EDM is particularly effective for hard metals and is extensively used in the aerospace, automotive, and tool-making industries.
Laser Machining
Another critical technique, laser machining employs high-energy laser beams to cut, weld, or engrave materials with extreme precision. Its non-contact nature minimizes thermal distortion, making it ideal for applications requiring ultra-fine detail, such as electronics, medical devices, and microfabrication. This versatility allows laser machining to work on a wide range of materials, including metals, plastics, and ceramics.
Grinding and Polishing
Both grinding and polishing are essential for achieving superior surface finishes and tight dimensional tolerances. Grinding removes excess material to refine the shape of a component, while polishing enhances its surface smoothness. These processes are crucial for applications like medical implants, optical lenses, and engine components, where smooth finishes and precise dimensions are critical to functionality and performance.
Metrology and Inspection
A close inspection plays a crucial role in guaranteeing the quality and precision of manufactured components. Advanced tools like Coordinate Measuring Machines (CMMs), laser scanners, 3D scanners, and optical comparators verify that the components meet exact specifications. By identifying errors early, these processes improve consistency, reduce waste, and maintain compliance with industry standards.
3 Peculiar Challenges in Precision Machining for Castings
Precision machining for castings presents several unique challenges. In order to safely overcome these, you must have an understanding of their causes. Here’s an insight into the obstacles of precision machining for castings and how to overcome them.
Porosity
Porosity occurs when air or gas becomes trapped in the casting during the manufacturing process, leading to internal voids. These voids compromise the structural integrity of the casting, resulting in weakened mechanical properties and issues like leaks in pressure-sensitive applications. When machining porous castings, uneven material density can lead to poor surface finishes and reduced precision.
To address this, manufacturers use non-destructive testing (NDT) techniques like X-ray radiography to detect porosity early. Additionally, vacuum impregnation can seal these voids, improving the casting's integrity. Specialized cutting tools and adaptive machining systems are also used to handle uneven material density effectively.
Residual Stresses
Within the casting, residual stresses are caused by uneven cooling during solidification. These stresses can lead to warping or distortion when the material is removed during machining, compromising dimensional accuracy and requiring costly rework. To mitigate residual stresses, heat treatment or vibration stress-relief processes can be applied before machining.
A roughing and finishing machining approach is often employed, where bulk material is removed in an initial pass, allowing the casting to stabilize before a precision finishing pass. Secure fixturing systems also play a critical role, ensuring that the casting remains stable and distortion is minimized during the machining process.
Inconsistent material hardness
Another common challenge in machining castings is inconsistent harnesses. Variations in hardness arise from differences in cooling rates or the presence of impurities in the material. This inconsistency can lead to uneven cutting forces, accelerated tool wear, chatter, and challenges in achieving uniform surface finishes.
Cutting tools made from wear-resistant materials like carbide or polycrystalline diamond (PCD) are used to handle hard spots effectively. Additionally, adaptive machining systems enable real-time adjustments to cutting speeds and feed rates based on material feedback. Refining the casting process, such as promoting uniform cooling, also helps minimize hardness variability and ensures more consistent machinability.
Sevenloop offers a promising solution to many challenges in precision machining for castings. With deep expertise in machining operations and by utilizing advanced technologies like multi-axis CNC machining and 3D scanning, Sevenloop enables faster production of complex components with minimal material waste. Our ability to precisely control surface structure, finish, and tolerance levels minimizes issues like porosity and material inconsistencies. Additionally, our technology suits the manufacturing of customized parts across different batch sizes, offering a cost-effective alternative to conventional casting and machining processes.
Conclusion
The art of precision machining for castings is a testament to human ingenuity and technological innovation, transforming raw materials into functional, high-performance components. These parts are essential across various industries, from landing gears and surgical equipment to heavy machinery. As demand for precision grows, so does the need for skilled professionals and advanced technologies to push the boundaries of what's possible.
This is where Sevenloop steps in—offering cutting-edge solutions that not only enhance precision but also enable greater design flexibility and material efficiency. Whether you're developing next-generation engines, crafting life-saving medical devices, or building durable industrial equipment, partnering with Sevenloop can elevate your success, by providing faster, more precise, and cost-effective solutions.