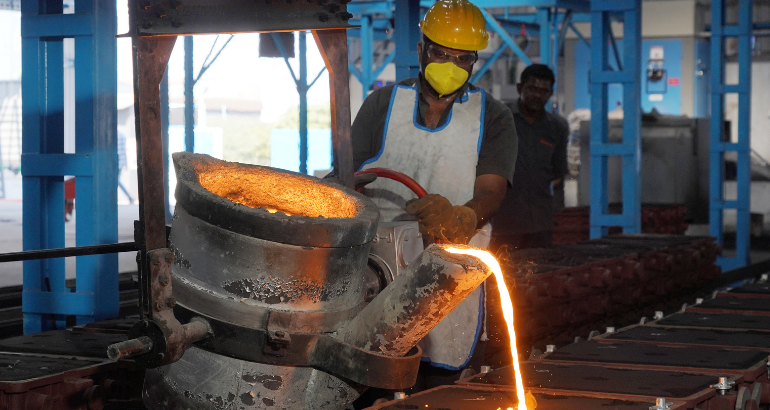
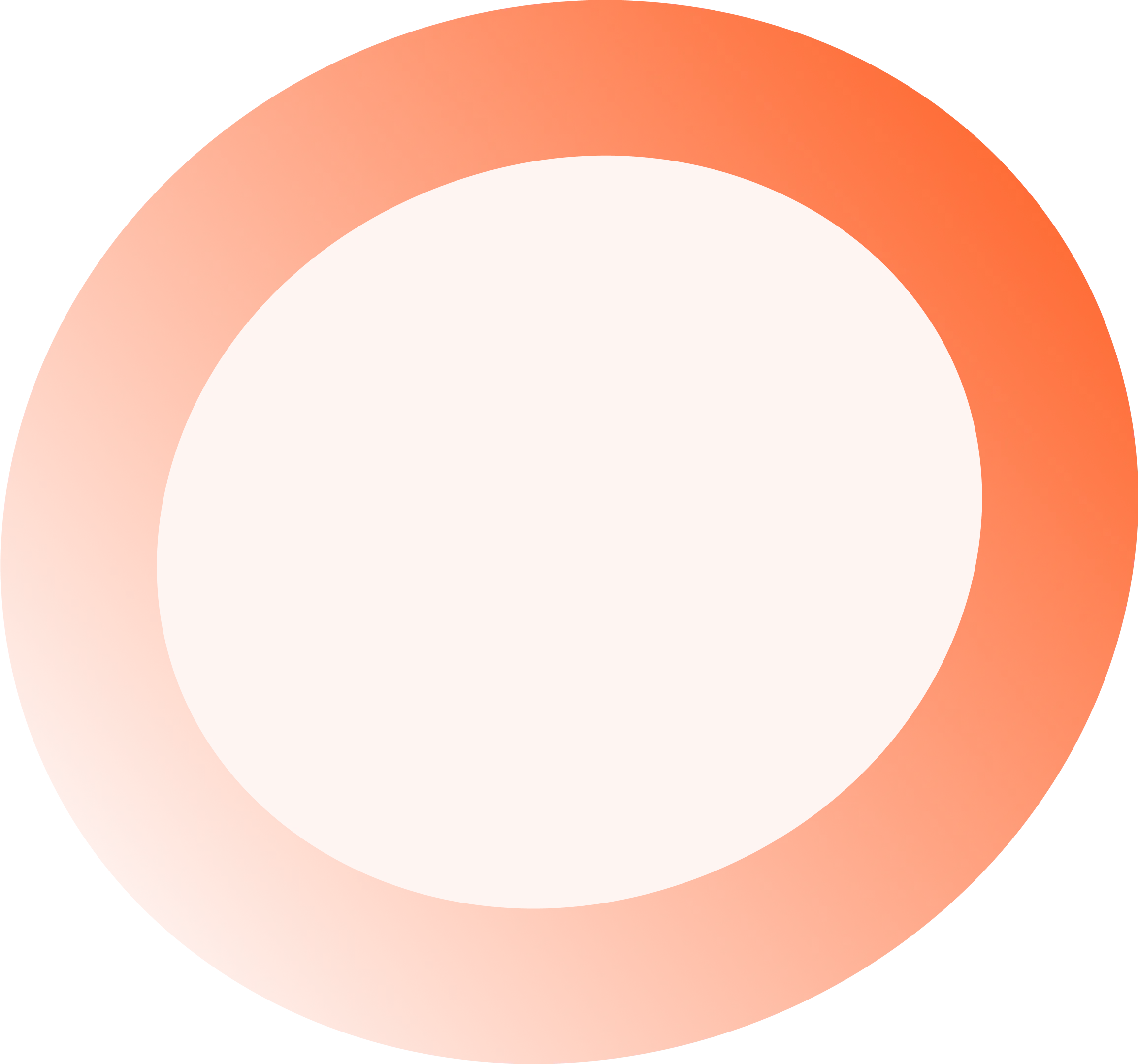
10 Best Practices for Foundries to Control rejections
Are you looking for ways to minimize rejections of your foundry products?
In the world of foundries, every rejected casting tells a story of untapped potential and avoidable losses. From process hiccups to material flaws, these challenges not only impact profitability but also ripple into customer trust.
However, by making seemingly small changes in your operations, you can easily eliminate a large number of rejections. Isn’t that fascinating?
The reasoning is quite simple. More often than not, these rejections are deeply rooted in the very processes that shape the products—whether it's inconsistencies in execution, subpar material handling, or operational inefficiencies. By refining these critical stages, you can not only lower rejection rates but also boost the overall quality of your products.
Let’s dive into some proven methods and strategies you can integrate into your foundry operations to achieve lower rejection rates.
10 Ways Foundries Can Reduce Rejections
Reducing rejections in foundries is not just about fixing flaws—it’s about building robust processes that prevent issues before they arise. By adopting a set of tried and tested practices, you can observe a noticeable difference in the rejection rate of your foundry’s products. Best practices for minimizing rejections focus on streamlining operations, ensuring material consistency, and maintaining process control at every stage.
1. Implementing Rigorous Raw Material Quality Control
The foundation of any high-quality casting lies in the raw materials used. Poor-quality inputs directly translate to casting defects. Conduct rigorous chemical and physical property testing for incoming raw materials like sand, metals, binders, etc. Additionally, using calibrated moisture meters for green sand systems brings about contamination-free storage conditions for metals or other additives.
Ensuring compliance with material specifications guarantees high-quality products. However, you must pay attention to your suppliers as well. As per SQA (Supplier Quality Assurance) establishing long-term partnerships with reliable suppliers, and performing regular audits help you maintain consistent material quality.
2. Optimizing Sand Control and Management
Sand systems are a critical component of many foundries, particularly those using green sand or chemically bonded sand. Defects such as sand inclusions, erosion, and poor surface finish often originate from inadequate sand management. In order to eliminate such errors, you must test sand at different stages of the process.
Regularly testing parameters like grain size, permeability, and compactibility help you start the process on a strong foot. When it comes to the durability of the end product, maintaining optimal levels of bentonite, coal dust, or other additives does an exceptional job. Along with durability, you can also count on this practice to balance the strength, collapsibility, and thermal resistance of the product.
If you’re looking to improve sand consistency, investing in mechanical or thermal sand reclamation systems is your go-to solution. This investment will not only enhance consistency but will also support waste reduction while lowering production costs.
3. Controlling Melting and Pouring Processes
The melting and pouring stages are crucial for producing defect-free castings, as inconsistencies here can cause shrinkage, porosity, or inclusions. Optimizing the melting process involves controlling furnace parameters—temperature, slag removal, and alloying—while using thermal analysis for precise metal composition.
Consistent pouring temperatures are vital to prevent turbulence and oxide formation, which can compromise the structural integrity of castings. To achieve this, preheating ladles is often suggested as it avoids sudden temperature drops during pouring. Additionally, you must ensure that the molten metal is poured steadily at the recommended speed and height.
In order to avoid excessive turbulence, you must use proper pouring angles and controlled flow rates, which minimize air entrapment. Incorporating pouring cups or sprue systems with smooth contours can further regulate the metal flow. To further enhance quality, you can also consider solutions like rotary degassing or ceramic foam filters to effectively minimize non-metallic inclusions.
4. Adopting Robust Pattern and Mold Management
Patterns and molds play a significant role in determining casting quality. Poor design or maintenance can result in dimensional inaccuracies, misruns, or fins. Using CAD software for designing patterns ensures precisely draft angles, risers, and gating systems. You can also leverage simulation-based validations for refining the designs before production.
By conducting regular inspections along with timely reconditioning of molds to maintain precision, you can prevent molds from wearing down. When it comes to issues like shrinkage or porosity, the resolution can be optimizing the vent and riser placements. This practice promotes smooth metal flow as well as effective gas escape which in turn reduces the chances of shrinkage.
5. Leveraging Simulation and Predictive Tools
Casting simulation software has revolutionized the foundry industry by allowing virtual trials before actual production. As a result, you can not only predict defects but also take necessary steps to prevent them. You can also look into software solutions that identify issues such as hot spots, shrinkage, and flow turbulence.
Such software systems allow you to make precise adjustments to gating systems, risers, mold designs, etc without the need for costly physical trials. By using the combined force of data from previous records and AI-driven analysis, simulations empower your foundry to make informed decisions.
6. Strengthening Process Control
A stable, well-controlled process enhances casting quality by reducing variability. You can leverage tools for Statistical Process Control (SPC) as they are quite precise in tracking parameters like temperature, pressure, and chemical composition. As a result, you can respond quickly to any deviation taking place, preventing small issues from escalating into costly rejections.
Having a detailed set of Standard Operating Procedures (SOPs) in place for each stage ensures consistency, laying the foundation for repeatable success. Meanwhile, regular training equips operators with the skills required to maintain process discipline, adapt to challenges, and implement defect prevention techniques effectively.
7. Conducting Comprehensive Non-Destructive Testing (NDT)
Non-destructive testing is vital for a number of reasons, from identifying sub-surface defects to ensuring compliance with quality standards. Common NDT methods like radiography, ultrasonic testing, and dye penetrant inspection are essential for detecting internal voids, cracks, or inclusions.
You can also consider integrating automated NDT systems directly into the production line. With such a system in place, you can identify defects in real-time as well as prevent delays. However, you must verify that the personnel are certified in these techniques. Moreover, staying up to date with the latest advancements strengthens the overall quality control process, helping to maintain consistent, defect-free castings.
8. Addressing Core and Shell Defects
Core-related defects like veining, blowholes, or dimensional inaccuracies can significantly impact casting quality. Effective core design as well as venting are crucial for minimizing stress concentrations. Such practices also ensure proper gas release during casting, eliminating blowholes.
Optimizing the type and amount of binder balances core strength with collapsibility, reducing the risk of defects. Proper storage under controlled humidity and temperature conditions prevents premature curing or damage. As a result, your cores perform reliably in production.
9. Utilizing Automation and Digitalization
Modern foundries are increasingly adopting Industry 4.0 technologies to enhance precision while minimizing human errors. Robotic molding and pouring systems ensure consistent results, reducing variability. IoT-enabled sensors provide real-time monitoring of critical parameters, enabling proactive adjustments to maintain quality.
Advanced ERP and MES systems digitize production data, offering valuable insights into operations. Analyzing this data helps identify top failure reasons, trace patterns, and even predict potential issues before escalation. Digital twin technology further supports these efforts by creating virtual replicas of foundry processes, allowing for testing as well as optimization with minimal disruptions. These technologies pave the way for smarter predictive production processes.
10. Conducting Regular Audits and Reviews
Frequent audits are essential to ensure that all the operations are aligned with quality objectives. Regular internal audits are also a great initiative to guarantee compliance with standard procedures as they often uncover opportunities for improvement. Inviting customers for audits not only fosters transparency but also verifies their quality expectations.
Pursuing third-party certifications like ISO 9001 or IATF 16949 boosts customer confidence while validating quality management systems. Together, these practices create a robust framework for continuous improvement, improving the qualitative standards in foundry operations.
Closing Thought
Reducing rejections in foundries is not just about eliminating defects but fostering a culture of quality, innovation, and efficiency. By implementing these best practices—ranging from material control to automation—foundries can achieve higher productivity, lower costs, and superior customer satisfaction. The journey toward zero defects requires a holistic approach, combining technical expertise with disciplined execution across every stage of production. When quality becomes a cornerstone of your operations, the benefits ripple across every aspect of your business.